Looking back on 2023, the global economy had been gradually stepping away from the impacts of COVID-19, and the production order was also recovering. The operational pressure for our company has significantly decreased, coupled with the quarterly decline in material prices, resulting in a significant improvement in the Company’s operation and profitability in 2023. However, affected by the global inflation, manufacturing sectors in most developed countries, such as Europe and the United States, are still in a sluggish state, keeping the general consumer demand relatively low.
Looking ahead to 2024, despite the global impact of inflation, the operating environment has been gradually recovering. The Company’s past new development projects and the construction of Baishan II will continue to contribute to a growing profit. Additionally, the Company will enhance its management and production technology while diversifying risks for customers. With professional manufacturing capabilities and a high-quality service concept, the Company is working towards securing new orders from domestic and foreign customers, actively pursuing the following goals:
Creating Values through Solid Corporate Governance
To align with the policy of the Financial Supervisory Commission, Eurocharm has launched “Corporate Governance 3.0 – Sustainable Development Blueprint.” Based on robust corporate governance, our company actively delivers high-quality and diversified precision machinery to customers by applying advanced manufacturing technology and comprehensive solutions tailored to meet their specific product needs. Eurocharm aims to maximize benefits for shareholders and foster the development of its employees. We aspire to become an esteemed enterprise trusted by society, maintaining strong interactions with stakeholders, and consistently creating corporate value.
Constant Promotion of Smart Manufacturing
Since 1983, Eurocharm has been utilizing welding robots and continuously introducing automatic production. During the Industry 4.0 era, we have been constantly progressing. The Company focuses on building intelligent production systems, equipment, and management process based on data. By integrating design, production, and services, we have successfully reduced costs, improved manufacturing efficiency, and enhanced product quality and customer experience, contributing to advancements in the industrial landscape. Moving forward, Eurocharm will further develop automation by implementing TOYOTA lean production principles. This involves optimizing the system structure, personnel organization, operational methods, and market supply and demand. We will also integrate the MES project to ensure our production system can quickly adapt to changing demands, eliminating unnecessary processes and strengthening our production management model.
Mitigating the Environmental Impact
COP28, also known as the United Nations Climate Change Conference, kicked off on November 30, 2023, in the United Arab Emirates (UAE), one of the world’s top ten oil-producing countries. This marked the first “Global Stocktake” in eight years since the 2015 Paris Agreement, reviewing the climate actions of 200 countries. The purpose of the Global Stocktake is to ensure that countries not only commit to their NDCs and submit plans but also to verify if they are on track to meet their commitments. As a responsible corporate citizen, Eurocharm initiated a group-wide greenhouse gas inventory in September 2022 and completed the inventory for 2022 in June 2023. We are committed to continuing carbon reduction efforts to mitigate the impacts of climate change on businesses. Additionally, we are actively evaluating the feasibility of solar energy installation to align with the global need for a rapid transition to clean energy, aiming to significantly reduce greenhouse gas emissions by 2030.
Providing a Friendly Environment and Ensuring Employee Health and Industrial Safety
Our environmental improvement and equipment replacement projects are being carried out for noise, dust, air, sewage treatment systems, lighting, and electric furnace usage. We will also strive to maintain our factories as green facilities and work towards energy conservation and carbon reduction goals. Simultaneously, we are continuously implementing significant changes in employee engagement, safe production practices, work environment enhancement, quality improvement, reduced delivery times, decreased non-productive working hours, and enhanced employee compensation and benefits. Our objective is to enhance the cohesion of the factory, improve internal management, and continually enhance our work environment and labor conditions to safeguard the legal rights of our employees and create a workplace that brings them happiness.
Diversity, Inclusion, and Cultivation of International Talents
Diversity, Equity, and Inclusion (DEI) has become a mainstream trend among multinational corporations, inevitably facing this wave in the era of globalization. We aim to embrace a more diverse range of perspectives as well as to effectively cultivate proactive problem-solving abilities and international viewpoints among all levels of management. The Company continues to collaborate with external experts to develop training programs tailored to individual traits and job attributes, aiming to cultivate and retain outstanding management and technical talents. This focus lays a more solid foundation for the Company’s sustainable development. Looking ahead, we will continue to actively expand into leisure vehicle components and medical equipment and pursue international strategies, ensuring sustainable growth in performance and profits. Meanwhile, we will adhere to the sustainable strategy blueprint, fulfilling corporate responsibilities to achieve sustainable operations.
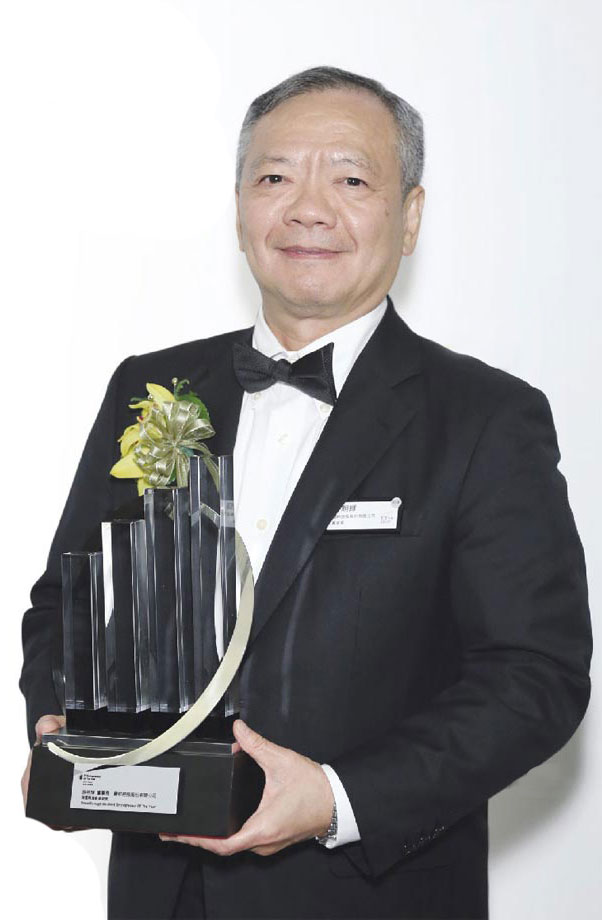